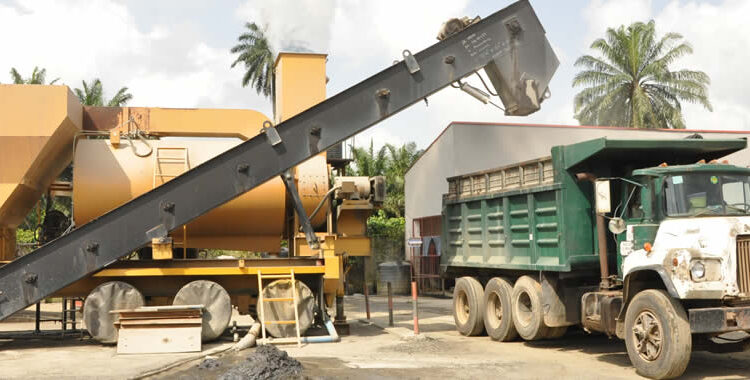
Asphalt Unity Construction see the benefits of going mobile with the help from Sandvik Mobiles
With the growing demand for construction materials in Nigeria, Asphalt Unity Construction turned once again to Sandvik Construction in order to help them achieve their increased production capacity.
Asphalt Unity Construction, based in Nigeria, started in 2009 and are a multifaceted engineering firm. Young, dynamic and vastly experienced engineers from different establishments came together to put their knowledge and experience to work.
Their aim was to deliver high quality engineering services for their clients, utilising competent personnel and good quality equipment. Now they have become one of the leading construction companies in the eastern region.
With such a focus on delivering high quality, in recent years they have looked to become smarter and more competitive in the industry. Having already experienced what Sandvik stationary crushers can produce, they decided to consider the Sandvik Mobiles portfolio to help them achieve their annual production target and to meet the demands in the Nigerian Delta State.
Mr. Mario El Fadi, Director of Asphalt Unity Construction, visited the Mobiles production facility in Swadlincote, Derbyshire back in September last year and was accompanied by Marshall John, Business Line Manager for Sandvik Construction in Nigeria. During his visit, Mr. El Fadi was able to see the benefits offered by the mobile plant and a er seeking knowledge from key product specialists at the factory, consequently placed an order for five tracked units.
Sandvik Mobiles offer a huge amount of flexibility, with quick set up mes and reliability. Mr. El Fadi commented “We wanted a quick win situation in order to achieve our targeted capacity and one of the huge advantages of mobile equipment is that no installation is required. We are able to quickly set the equipment up and start production almost immediately.”
With the mobiles working alongside the stationary models, Asphalt Unity Construction could also benefit from using one set of parts, helping them to keep costs to a minimum.
Their application is crushing basalt and granite to be sold on to building contractors. Basalt is most commonly crushed for use as an aggregate in construction projects such as road base, concrete aggregate, asphalt pavement aggregate and railroad ballast. Granite has been used for thousands of years in exterior applications and rough‐cut and polished granite can be used in buildings, bridges and paving.
To meet their high capacity requirements of up to 700mtph, Asphalt Unity Construction chose from the Sandvik Mobiles heavy duty (HD) and extra heavy duty (XHD) porolio and selected the UJ640 jaw and US440i and UH640 cone crushers to work alongside two QA451 Doublescreens.
The required product sizes are 0‐25mm and 0‐35mm so the combination of jaw and cone crusher means the abrasive material can be broken down easily to these levels, with the jaw breaking down the material and the cone providing shaping.
The UJ640 is a tracked jaw crusher that has been purpose designed for the global aggregates industry, and features the Sandvik CJ615 jaw, single toggle 1500 x 1100 mm / 60 x 44”, which allows for enormous rates of production with a 975mm (38”) maximum feed size.
Working alongside the jaw are the US440i and UH640 cone crushers. The US440i is the ultimate HD cone crusher capable of accepng a feed size of up to 450mm (18”). Designed for the large mine or quarry operator, the US440i allows Asphalt Unity Construction to maximise their primary jaw production by opening CSS for maximum throughput. It also features the market leading Sandvik CS440 cone crusher and comes with a wide choice of mantles and sengs making it suitable for a huge range of different applicaons worldwide. Similarly, the UH640 is a flexible, highly productive secondary or Tertiary cone crusher that is able to produce finished sized products thanks to an integral product screen and closed circuit operation. It also accepts a maximum feed size of 235mm (9”).
One of the keys to the high productivity and efficiency is the automatic seng system, ASRi, on the cones which optimizes the crushing process. The ASRi also assists in keeping the crusher choke fed in order to maximize rock‐on‐rock crushing, which helps ensure the highest quality end product.
The plant also ulises a QA451, the world’s only triple deck Doublescreen featuring two inline 10′ x 5′ screenboxes for unrivalled throughput and control, designed specifically to work in closed circuit with tracked crushers. The hydraulically folding fourth product conveyor slews and raises / lowers hydraulically to optimise the feeding posion to these upstream units.
Utilising Sandvik’s unique patented Doublescreen technology, the advanced triple deck Doublescreen system allows for individual changes to the drive, angling, vibration and meshes of each screen box, which allows for ultimate versatility in size and specification of the finished products.
Following the success of this application, Asphalt Unity Construction are looking to expand their fleet of machines to help them reach a new goal of 1,500t/h and with high production capacity machines available, the Sandvik Mobiles product range will put them in the ideal position.
With the growing demand for construction materials in Nigeria, Asphalt Unity Construction turned once again to Sandvik Construction in order to help them achieve their increased production capacity.
Asphalt Unity Construction, based in Nigeria, started in 2009 and are a multifaceted engineering firm. Young, dynamic and vastly experienced engineers from different establishments came together to put their knowledge and experience to work.
Their aim was to deliver high quality engineering services for their clients, utilising competent personnel and good quality equipment. Now they have become one of the leading construction companies in the eastern region.
With such a focus on delivering high quality, in recent years they have looked to become smarter and more competitive in the industry. Having already experienced what Sandvik stationary crushers can produce, they decided to consider the Sandvik Mobiles portfolio to help them achieve their annual production target and to meet the demands in the Nigerian Delta State.
Mr. Mario El Fadi, Director of Asphalt Unity Construction, visited the Mobiles production facility in Swadlincote, Derbyshire back in September last year and was accompanied by Marshall John, Business Line Manager for Sandvik Construction in Nigeria. During his visit, Mr. El Fadi was able to see the benefits offered by the mobile plant and a er seeking knowledge from key product specialists at the factory, consequently placed an order for five tracked units.
Sandvik Mobiles offer a huge amount of flexibility, with quick set up mes and reliability. Mr. El Fadi commented “We wanted a quick win situation in order to achieve our targeted capacity and one of the huge advantages of mobile equipment is that no installation is required. We are able to quickly set the equipment up and start production almost immediately.”
With the mobiles working alongside the stationary models, Asphalt Unity Construction could also benefit from using one set of parts, helping them to keep costs to a minimum.
Their application is crushing basalt and granite to be sold on to building contractors. Basalt is most commonly crushed for use as an aggregate in construction projects such as road base, concrete aggregate, asphalt pavement aggregate and railroad ballast. Granite has been used for thousands of years in exterior applications and rough‐cut and polished granite can be used in buildings, bridges and paving.
To meet their high capacity requirements of up to 700mtph, Asphalt Unity Construction chose from the Sandvik Mobiles heavy duty (HD) and extra heavy duty (XHD) porolio and selected the UJ640 jaw and US440i and UH640 cone crushers to work alongside two QA451 Doublescreens.
The required product sizes are 0‐25mm and 0‐35mm so the combination of jaw and cone crusher means the abrasive material can be broken down easily to these levels, with the jaw breaking down the material and the cone providing shaping.
The UJ640 is a tracked jaw crusher that has been purpose designed for the global aggregates industry, and features the Sandvik CJ615 jaw, single toggle 1500 x 1100 mm / 60 x 44”, which allows for enormous rates of production with a 975mm (38”) maximum feed size.
Working alongside the jaw are the US440i and UH640 cone crushers. The US440i is the ultimate HD cone crusher capable of accepng a feed size of up to 450mm (18”). Designed for the large mine or quarry operator, the US440i allows Asphalt Unity Construction to maximise their primary jaw production by opening CSS for maximum throughput. It also features the market leading Sandvik CS440 cone crusher and comes with a wide choice of mantles and sengs making it suitable for a huge range of different applicaons worldwide. Similarly, the UH640 is a flexible, highly productive secondary or Tertiary cone crusher that is able to produce finished sized products thanks to an integral product screen and closed circuit operation. It also accepts a maximum feed size of 235mm (9”).
One of the keys to the high productivity and efficiency is the automatic seng system, ASRi, on the cones which optimizes the crushing process. The ASRi also assists in keeping the crusher choke fed in order to maximize rock‐on‐rock crushing, which helps ensure the highest quality end product.
The plant also ulises a QA451, the world’s only triple deck Doublescreen featuring two inline 10′ x 5′ screenboxes for unrivalled throughput and control, designed specifically to work in closed circuit with tracked crushers. The hydraulically folding fourth product conveyor slews and raises / lowers hydraulically to optimise the feeding posion to these upstream units.
Utilising Sandvik’s unique patented Doublescreen technology, the advanced triple deck Doublescreen system allows for individual changes to the drive, angling, vibration and meshes of each screen box, which allows for ultimate versatility in size and specification of the finished products.
Following the success of this application, Asphalt Unity Construction are looking to expand their fleet of machines to help them reach a new goal of 1,500t/h and with high production capacity machines available, the Sandvik Mobiles product range will put them in the ideal position.